Maintenance of the Rotate Tablet Press Machine
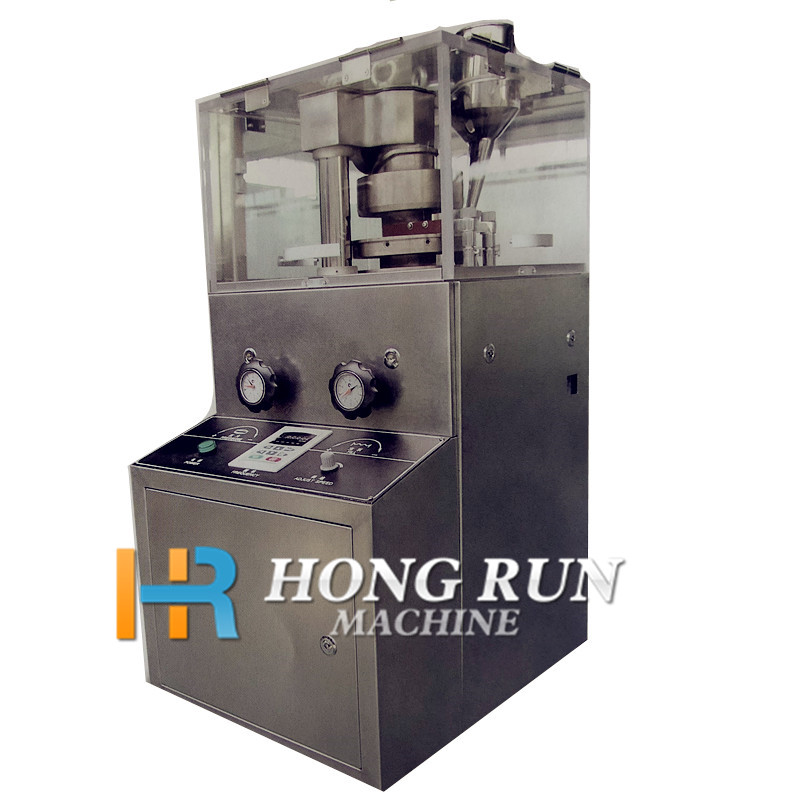
(1) The irregular length of punches can easily lead to the increase of the difference in sheet weight. Therefore, before using the caliper, each punch will be checked up and reused after passing the test. If there are individual decreases, the downrush movement may fail, resulting in less filling of particles than the others. Individual downrush should be checked out to remove obstacles.
(2) Incorrect high and low device of feeding hopper can result in fast dropping of particles in one feeding hopper, while more particles are accumulated on the feeder and slower dropping of particles in the other hopper, while fewer particles are accumulated on the feeder, resulting in unbalance of particles when they are added to the die holes. The position of feeding hopper can be adjusted so that the particles in the two feeding hoppers should keep a certain number and fall. At the same speed, the particles accumulated on the two feeders are similar, and the particles can be evenly added into the die hole.
(3) The change of wafer weight caused by particles, excessive wetting of particles, excessive fine powder, excessive difference in particle size and insufficient lubricant in particles can also cause the change of wafer weight differential conductivity, and the quality of particles should be improved.
(4) The reason for the change of sheet weight is that the general situation is caused by the breakdown of the tablet press or negligence in work. Therefore, during the process of pressing, the maintenance of the parts should be done, the parts should be checked carefully, and weighed every certain time (10-20 minutes). Whether the sheet weight is in accordance with the regulations or not should be checked carefully.